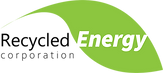
Technology

Catalytic Depolymerization Explained
The catalytic depolymerization technology breaks long chain molecules comprised of carbon and hydrogen atoms into shorter chain hydrocarbons by using a unique catalyst that allows the depolymerization (cracking) of the molecules by breaking bonds between the atoms. A second part of the process creates excess hydrogen that is available to bond with carbon molecules to “close off” the molecules into hydrocarbon chains.
The shorter chain molecules are carbon and hydrogen, called hydrocarbons, typically in the range of C1 to C22 for gaseous and liquid hydrocarbons. The hydrocarbon chains will continue to depolymerize until the shorter chain molecules evaporate. Just as water will evaporate at 100 degrees C. and become steam, the hydrocarbons will evaporate into hydrocarbon gasses at temperatures from 100 degrees C up to 300 degrees C (for our purposes). These hydrocarbon gasses are cooled and separated via a distillation column where the reduction in gas temperature causes the gasses to form liquid hydrocarbon similar to Diesel fuel. This again, is just like when water becomes steam, then the steam is cooled, it becomes water again.
Pyrolysis Explained
Pyrolysis occurs in a sealed vessel which is devoid of oxygen and heated from the outside. When heated in the vessel, waste materials de-polymerize – the molecules forming the waste detach from each other to produce syngas, which has properties similar to natural gas. The gasses created by this controlled heating and depolymerization of waste materials are condensed into fuel. The solids are separated into carbon and recovered metals.

REC’s environmentally responsible process introduces feedstock through an airlock into a closed loop system. The carbon black, recovered metals and fuel exit the pyrolysis system through airlocks and valves which prevent oxygen from entering the vessel. Non-condensable gasses re-circulate through the system, causing further feedstock depolymerization and aiding fuel formation. REC's tightly controlled zero oxygen environment prevents the formation of dioxins, furans and other harmful compounds – a significant advantage over gasification and incineration.

Inputs and Outputs
The catalytic depolymerization technology can convert any organic or carbon-bearing feedstock material into Renewable Diesel. A pictorial of the technology is shown.
Shredding and Drying
-
The feedstock needs to be shredded and dried to 100 micron and 10% moisture content.
-
The shredding and drying is done mechanically instead of using applied heat.
-
This saves energy as generating heat requires much more energy than doing the processing mechanically.
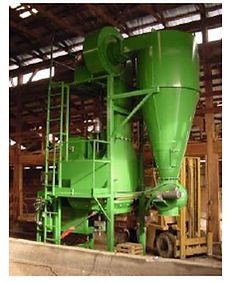


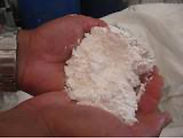
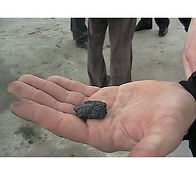
Renewable Diesel Fuel Qualities
REC’s depolymerization technologies will produce very high quality fuel. It meets the low sulfur requirements for the US and European standard Diesel fuel specifications. The fuel meets all other specifications for ASTM D975 (US Diesel fuel specification). Because the input materials are non-petroleum and from a renewable biomass source, it qualifies as a Renewable Diesel fuel. We can also choose to make #2 Diesel (normal Diesel) or we can make #1 Diesel (winter Diesel – a lighter version of Diesel).
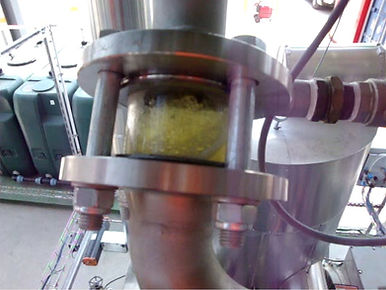

Catalyst
-
Used for 70 years in refineries
-
Crystalline shape zeolite catalyst-
-
Aluminum Silicate material-
-
Causes depolymerization with high agitation, no pressure, and hydrocarbons are produced at under 300 degrees C.
-
Combines with heavy metals on a molecular basis to form salts-
-
Non-leachable/insoluble ash is formed as the catalyst combines with the heavy metals